Diesel Generator Performance Testing Ensuring Reliable Power Generation
Introduction
Diesel generators have been a crucial component of power generation systems for decades, providing reliable backup power during grid outages or serving as the primary power source in remote locations. To ensure their optimal performance and reliability, regular performance testing is essential. Performance testing of diesel generators involves evaluating various parameters and characteristics to ensure they meet the required standards and specifications. This article explores the importance of performance testing for diesel generators, the key parameters to be evaluated, testing methods, and best practices to ensure reliable power generation.
Importance of Performance Testing for Diesel Generators
Performance testing is critical for diesel generators to ensure their reliable operation during power outages or emergencies. By testing the generator under various load conditions, environmental factors, and operational scenarios, potential issues and weaknesses can be identified and addressed before they lead to system failures. Performance testing also helps in verifying the generator's compliance with regulatory standards, manufacturer specifications, and industry best practices.
Regular performance testing of diesel generators can also help in optimizing their efficiency and extending their lifespan. By monitoring key parameters such as fuel consumption, power output, emissions, and temperature levels during testing, operators can identify opportunities for improvement and maintenance. This proactive approach can prevent unexpected downtime, reduce repair costs, and enhance the overall reliability of the power generation system.
Key Parameters for Performance Testing
Performance testing of diesel generators involves evaluating a range of parameters to assess their functionality, efficiency, and reliability. Some of the key parameters that are commonly tested include:
1. Power Output: Power output testing involves measuring the generator's ability to deliver the specified electrical power output under different load conditions. This test helps in determining the generator's capacity and performance under varying demand levels.
2. Fuel Consumption: Fuel consumption testing is essential to evaluate the efficiency of the diesel generator in converting fuel into electrical power. By measuring fuel consumption at different load levels, operators can optimize fuel usage and reduce operational costs.
3. Voltage Regulation: Voltage regulation testing assesses the generator's ability to maintain a stable voltage output within acceptable limits under varying load conditions. Poor voltage regulation can lead to equipment damage and power quality issues.
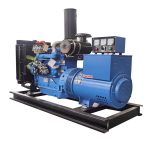
4. Frequency Regulation: Frequency regulation testing evaluates the generator's ability to maintain a stable frequency output within the specified range. Deviations in frequency can impact the performance of connected equipment and sensitive electronics.
5. Emissions: Emissions testing is crucial for diesel generators to ensure compliance with environmental regulations and emission standards. By monitoring 200kw diesel generator as nitrogen oxides (NOx), carbon monoxide (CO), and particulate matter, operators can mitigate environmental impact and ensure air quality standards are met.
6. Temperature Levels: Temperature testing involves monitoring the cooling system, engine, and electrical components for abnormal temperature levels during operation. Overheating can lead to system failures and component damage, highlighting the importance of temperature monitoring during performance testing.
Testing Methods for Diesel Generator Performance
Performance testing of diesel generators can be conducted using various methods depending on the specific requirements and objectives. Some of the common testing methods include:
1. Load Bank Testing: Load bank testing involves connecting an external load bank to the generator to simulate real-world operating conditions and load levels. This method helps in evaluating the generator's performance under different load scenarios and identifying potential issues related to power output, voltage regulation, and frequency control.
2. On-Load Testing: On-load testing involves conducting performance tests while the generator is supplying power to the load. This method provides real-time data on the generator's performance under actual operating conditions and helps in assessing its reliability and efficiency.
3. No-Load Testing: No-load testing is performed when the generator is disconnected from the load to evaluate its idle performance, starting capabilities, and voltage/frequency regulation. This test helps in verifying the generator's basic functionality and electrical parameters.
4. Operational Testing: Operational testing involves running the generator for an extended period under varying load conditions to assess its durability, stability, and overall performance. This method helps in identifying any issues related to overheating, fuel consumption, emissions, and noise levels.
Best Practices for Diesel Generator Performance Testing
To ensure effective performance testing of diesel generators and reliable power generation, operators should follow some best practices:
1. Regular Testing Schedule: Establish a regular testing schedule for diesel generators to monitor their performance, detect issues early, and prevent unexpected failures. Ideally, generators should be tested monthly or quarterly depending on their usage and criticality.
2. Document Test Results: Maintain detailed records of performance test results, including power output, fuel consumption, voltage/frequency regulation, emissions, and temperature levels. This documentation helps in tracking the generator's performance over time and identifying trends or anomalies.
3. Conduct Preventive Maintenance: Perform regular maintenance tasks such as oil changes, filter replacements, and cooling system checks to ensure the generator's optimal performance during testing. Addressing minor issues promptly can prevent major failures and downtime.
4. Calibration of Testing Equipment: Ensure that testing equipment such as load banks, voltage meters, and frequency counters are calibrated regularly to ensure accurate and reliable test results. Inaccurate measurements can lead to incorrect conclusions and potential risks.
5. Safety Precautions: Follow safety protocols and guidelines while conducting performance testing to prevent accidents, injuries, and equipment damage. Ensure that testing personnel are trained in safe operating practices and wear appropriate personal protective equipment.
6. Data Analysis and Reporting: Analyze the test data collected during performance testing to identify trends, anomalies, and areas for improvement. Prepare detailed reports highlighting the generator's performance metrics, test results, and recommendations for maintenance or upgrades.
Conclusion
Performance testing of diesel generators is essential for ensuring reliable power generation, compliance with standards, and optimal efficiency. By evaluating key parameters such as power output, fuel consumption, voltage regulation, and emissions, operators can identify issues early, optimize performance, and extend the lifespan of the power generation system. By following best practices, conducting regular testing, and maintaining accurate documentation, operators can enhance the reliability and resilience of diesel generators for critical applications. Effective performance testing is a proactive approach to mitigating risks, optimizing operations, and ensuring uninterrupted power supply when it is needed the most.